- Metal is treated by new high-power laser that ‘textures’ metal surface with microscopic spikes
- Rough micro topography acts like a bed of nails to stop dirt or liquid attaching
- Grease and bacteria never stick, meaning liquid and dirt simply roll off
The end of scrubbing ovens and home appliances with chemicals or heat could soon be in sight, thanks to a new high-power laser system being developed to put ‘self-cleaning’, grease-repellent and antibacterial properties into sheet metal. Teaming up with appliance giant Bosch, the European photonics consortium behind the laser system could soon see their technology create fluid-repellent surfaces fitted inside the next generation of dishwashers or fridges.
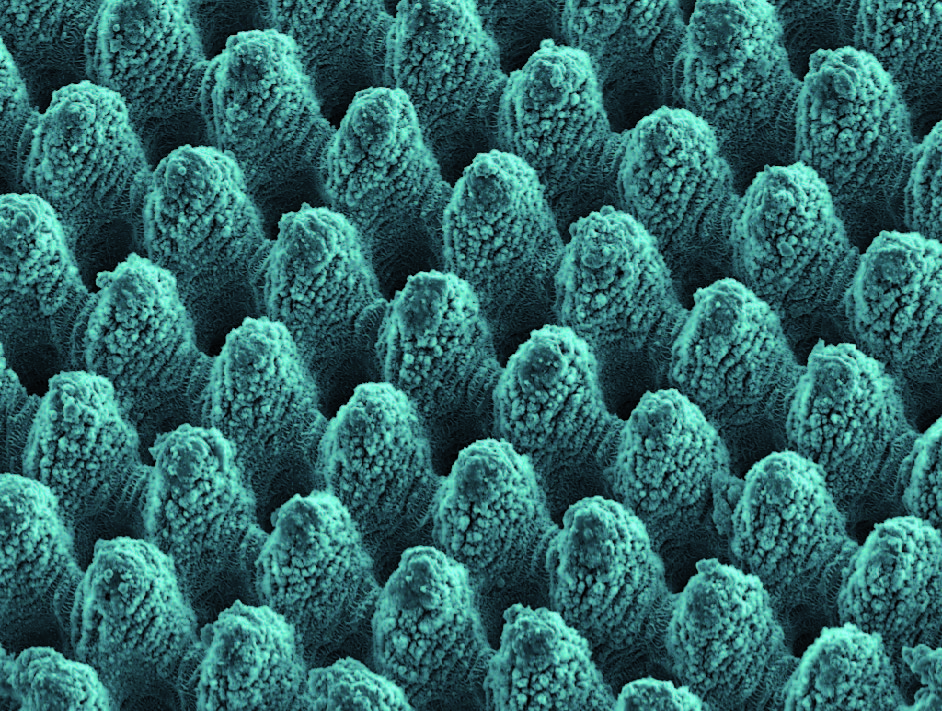
by new laser system.
Scrubbing worktops, unblocking your dishwasher or fatbergs building up in our sewers could be a thing of the past, thanks to new laser technology for structuring metallic surfaces, currently being developed by a European photonics consortium.
Preventing water, dirt or grease from ever attaching, the treated metal will mean fridges or oven doors remain clean for a longer period, without using detergents or heat.
‘Textured’ by some of the most powerful lasers in the world, this new laser-treated metal will have microscopic 'spikes' or 'ridges' that act like a bed of nails and stop dirt or liquids attaching themselves.
The laser creates an 'amphiphobic' – or repellent to water and oils – surface upon the metal similar to the defence mechanisms found in nature like Lotus leaves or springtails' skin, enabling water and oil to simply 'roll off'. Similar micro-nano-structures reduce the build-up of bacteria meaning a surface never becomes dirty.
Although this work is currently being carried out on metal, the scientists say the laser-structuring technique works with other materials, like plastic and glass.
While we normally rely on surface coatings like Teflon to make easy-to-clean products, they can suffer from drawbacks if the covering breaks apart that can then emit toxic particles or gases.
The direct laser treatment of the surface – what the team calls 'surface functionalisation' or a way of altering the properties of the surface - therefore, provides an environmentally friendly and much safer alternative.
Teaming up with home appliance giant Bosch, the LAMpAS consortium is tailoring sheet metal to several different applications.
LAMpAS project coordinator Prof. Dr Andrés Fabian Lasagni said: "We are targeting related use cases: medical surfaces in hospitals, like stainless steel antibacterial surfaces; packaging machines in the pharma industry that need to be disinfected; machines in the food processing sector that need be continually cleaned and where hygiene is paramount."
Grease-Repellant
While sheet metal has previously been textured to repel water and bacteria, preventing fingerprints remains a novel approach for laser-treated metal. Carved specifically to repel grease and fat, the metal will have 'amphiphobic' properties, or the ability to repel water and oil simultaneously.
The Laser Technology Leader in the European Photonics Industry Consortium (EPIC) Dr Francesca Moglia said: "We are treating sheet metal to obtain what we at LAMpAS call 'anti-fingerprint' characteristics. If we use this metal on the outside of a refrigerator, an oven or kitchen surface, the user would not have to clean finger or hand marks so often – meaning your fridge always stays shiny.
"The treatment of surfaces with special laser radiation and beam transport systems to improve their antibacterial properties opens up new frontiers in applications. LAMpAS is using high-power ultrashort-pulsed lasers to create a rough micro-topography on sheet metal that will cause liquids to 'glide' across the surface, thus, reducing the formation of a biofilm.”
Micro Structuring with Photonics
Called 'LAMpAS' (short for the 'high throughput Laser structuring with Multiscale Periodic feature sizes for Advanced Surface Functionalities') the team is working on producing self-cleaning metal sheets on an industrial scale.
The metal surfaces are textured using industrial photonics devices: high-power, ultrashort-pulsed lasers are used in combination with high-performance scanning heads by utilising an innovative beam delivery method enabling movements of up to 100 m/s.
"The idea of using photonics or high-powered lasers to create tiny structures on metal is nothing new but has always been too expensive to produce and too time-consuming”.
"Our laser system will allow us to treat more than 1 square metre of sheet metal per minute covering a potentially growing market that could reach nine-digit revenues per year in the home-appliance sector alone. With our innovative Direct Laser Interference Pattering (DLIP) - Polygon Scanner head we will be able to treat metal with a 1.5 kW novel ps-laser source, with scanning speeds over 100 m/s," said Prof. Dr Lasagni.
At present, the LAMpAS team are focusing their expertise on flat metallic surfaces, but beyond the project see a broad market for large areas of other materials
"Anything that requires complete hygiene will benefit greatly from antibacterial surfaces such as hospital and operation environments that must be continually cleaned during surgical procedures."
Coordinated in Germany by the Technical University Dresden, the LAMpAS consortium has received a grant of € 5 121 692.50 from the European Union’s Horizon 2020 research and innovation programme under Grant Agreement No. 825132. It is an initiative of the Photonics Public Private Partnership.
LAMpAS includes members from many European organisations in countries including NEXT SCAN TECHNOLOGY BV, LASER ENGINEERING APPLICATIONS SA (Belgium); TRUMPF LASER GMBH, ROBERT BOSCH GMBH (Germany); the EUROPEAN PHOTONICS INDUSTRY CONSORTIUM (France); and BSH ELECTRODOMESTICOS ESPANA SA, NEW INFRARED TECHNOLOGIES SL (Spain).