Researchers at TalTech in Estonia push to produce biodegradable packaging from cellulose
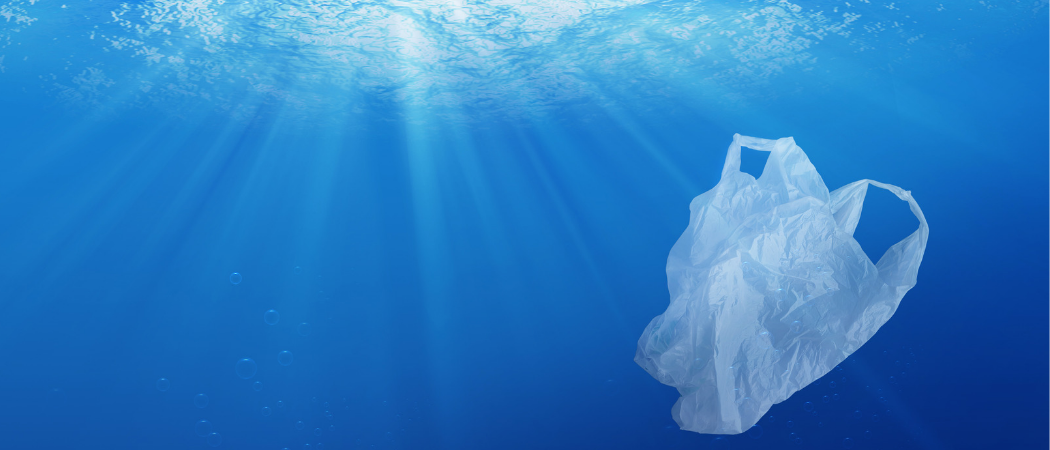
Pressure is building to find greener alternatives to plastic food packaging. While millions of tonnes of almost indestructible plastic enter the world’s oceans each year, malleable packing films are burned or sent to landfill after use, causing further pollution.
In an ideal world, the oil-based polymers used to pack food and drink would be swapped out for bio-based polymers that will quickly degrade without causing any harm to the natural environment. Andres Krumme, a professor in the Department of Materials and Environmental Technology, Tallinn University of Technology (TalTech) in Estonia, is trying to make that happen. “All of mankind is looking for a substitute for oil-based polymers,” he says. “Today, we are packing everything, including food, in polymers that can have a useful lifetime of 10 to 60 years.”
In their labs, Krumme’s research team has successfully developed a new type of cellulose-based polymers that can be melted and manipulated in the same way as low density polyethylene (a widely used packaging material), under conditions similar to those typically used in industrial polymer processing. “Cellulose biopolymer is generally highly crystallized with strong hydrogen bonds, which means it can’t easily be melted or processed,” explains Krumme. “But our new polymers - cellulose fatty acid esters– can be processed in the same way as the commodity polymers.” Moreover, he says the relatively easy modification procedure should make it possible to obtain other new polymers with a wide range of properties.
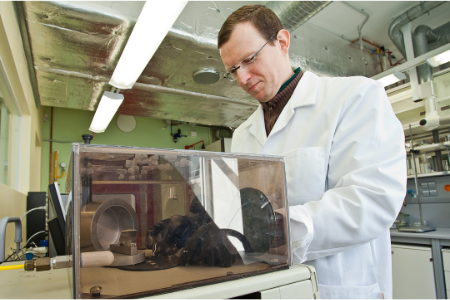
The most abundant polymer in the biosphere
As cellulose is the main constituent in the cell walls of all plants, these new polymers could be sourced from trees, algae and other vegetation grown on land that isn’t being used for agriculture. “Cellulose is the most abundant polymer in the biosphere,” notes Krumme. “If we could harness 0.4% of the cellulose produced in the biosphere we could replace all the plastic produced each year across all sectors – 350 million tonnes annually.” Today, bio-based polymers are produced at scale. But they are generally sourced from crops, cultivated with pesticides and fertilisers on land that could be farmed for food. As the global population rises inexorably, this approach may no longer be sustainable. In northern European countries, such as Estonia, agricultural land is limited, but forest cover is plentiful.
Another attractive feature of the new polymers Krumme is developing is they can be adjusted for various levels of permeability, he explains: “It can be a quite good barrier material – better than polyethylene. One can also adjust the ratio of biodegradability according to the useful lifetime of the packaging, which could be months, weeks or days.”
The roadmap to industrialisation
The Taltech researchers are now preparing to pilot the new process, which involves a reaction of aliphatic acid chlorides with cellulose in an ionic liquid, on a larger scale. Whereas his team has produced a few grams of these new polymers in their labs, it plans to produce a few kilograms in a pilot using a production line with a dedicated reactor.
Although his research over the past five years has been held back by a shortage of funding, Krumme is confident he can secure a grant for the pilot by early 2020. “Food packaging was not a high priority, but now one of the four new focus areas for Estonian research funding is food and another is wood, so I am optimistic the lab research can proceed to pilot,” he says. The research could also benefit from the falling price of the ionic liquids used in the chemical process. “The price of the ionic liquids we used in the labs was a few hundred euros per litre, but the chemical industry is developing cheaper alternatives and there are companies in Finland developing new textiles based on these solvent systems,” Krumme adds.
For the pilot, the labs’ existing equipment will need to be modified to achieve a higher degree of substitution of functional groups of cellulose, which was quite low in his initial research, Krumme says. However, he believes the new materials could already serve as strength-enhancing agents or as plasticizers and compatibilizers in polymer blends containing some commodity polymers and cellulose or wood fibres. “And there are now more efficient environments and we are quite optimistic that in one year maximum, we can overcome the substitution issue, so we can set up the pilot in 2021 and from there it would take between two and five years to progress to industrialisation,” Krumme explains.
Today, the new biopolymers would cost about twice as much to produce as their oil-based equivalents, according to Krumme. But that differential could come down as the production process is refined and, if and when, the price of oil-based polymers rises as a result of targeted taxes and/or the increasing cost of extracting fossil fuels. Cellulose-based polymers “could be a premium product that people who care about the environment are prepared to pay more for,” notes Krumme. “But the biggest user of plastics is Asia, where people are not willing or able to pay higher prices. We need to develop tech that makes it as cheap as possible.”
The cellulose-based polymers are likely to be used initially for packaging dry food products, such as grain, rather than fresh produce and meat. Packaging the latter would require special adaptations to ensure the moisture in the contents doesn’t biodegrade the packaging too fast. In a 2019 paper[1] reviewing the use of bio-based polymers for sustainable packaging and biobarriers, researchers at Aalto University in Finland noted that “both, wood and microorganism-derived biopolymers are challenged when moisture, grease and oxygen resistance are simultaneously required.” But the authors also noted that “novel cellulosic solvents” and “homogeneous modification methods” could lead to improved and more end-use-specific properties of the cellulose derivatives.
Once they perfect the chemistry, the Taltech researchers are confident that commercialisation will follow. “The food processing sector here in Estonia is very interested, so there should be a broad range of customers,” Krumme concludes. “And there are a few large companies in Estonia that are producing cellulose fibres for the paper industry who could want to partner on this. As a small country, Estonia, is a good test-bed for these technologies.”
[1] Helanto, K., Matikainen, L., Talja, R., and Rojas, O. J. (2019). "Bio-based polymers for sustainable packaging and biobarriers: A critical review," BioRes. 14(2), 4902-4951.