Greater use of nickel in batteries is increasing the range of electric vehicles, making them more attractive to consumers whilst providing incentives to recycle, says Mark Mistry, senior public policy manager of the Nickel Institute
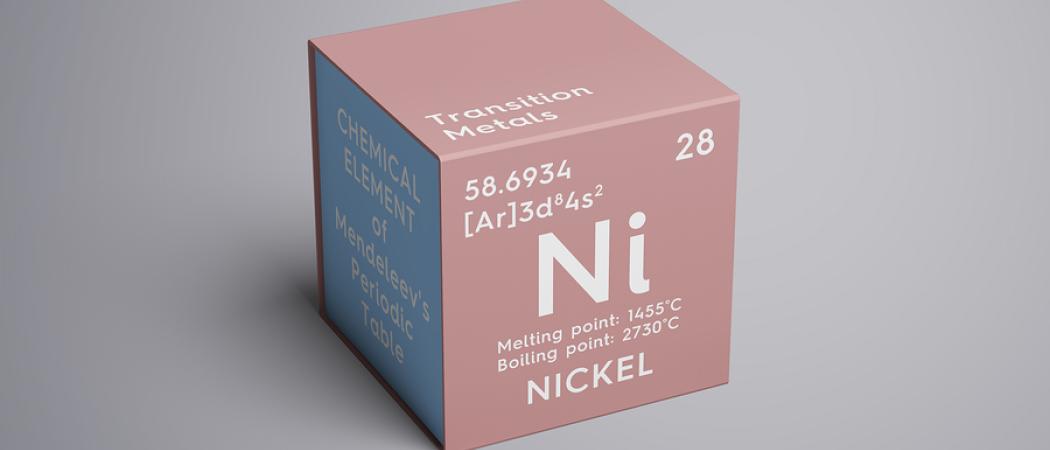
If electric vehicles are to deliver a sustainable transport system for the future their green credentials must be maximised across the whole life cycle.
That means that in addition to how a vehicle performs in service, the sourcing of raw materials, manufacturing and – crucially - how the parts are to be recycled, must be factored into the development of battery-powered vehicles.
Batteries - as the energy source - must be measured against fossil fuels not only in their far superior performance in engine emissions, but also in terms of the availability and cost of the raw material inputs, the manufacturing processes, and of the eventual disposal of spent batteries.
The development of a mass market in electric vehicles hangs on improvements in battery technologies to extend the range and reduce the time batteries take to recharge.
Batteries fitted in present-day electric vehicles are 100 per cent more efficient in terms of range than the previous generation. The next generation is expected to be 100 per cent better still.
But while such improvements are driving uptake of electric vehicles and global production of batteries to power them is growing strongly, it is critical to ensure this is sustainable.
That requirement has put the focus on rare earth metals including lithium and cobalt, which are in short supply and hard to recycle. Increased demand from battery manufacturers led to cobalt doubling in price in 2017.
However, in terms of raw material inputs, the amount of cobalt and other rare earth metals in batteries is falling, whilst the amount of nickel, which is already the single largest element in modern electronic vehicle batteries, is increasing.
That bodes well for the cost, the power and the incentives to recycle batteries, according to Mark Mistry, senior public policy manager of the Nickel Institute. The trend is to use more nickel whenever possible, because of its ability to increase battery power. “And nickel metal itself is fully recyclable without loss of quality,” Mistry noted. “It is not consumed in battery production or use.”
Nor will an increased demand for nickel lead to supply problems. “There is no shortage of nickel resources for making electric vehicle batteries,” said Mistry. “It is the fifth most common element on earth and occurs extensively in the planet’s crust.”
Demand for nickel for electric vehicles is forecast to climb to around 500,000 tonnes by 2030 according to a study by metals market analyst Roskill. “Since current global production of nickel is about two million tonnes per annum, there is really no problem with resource availability.” Mistry said.
Even if demand turns out to be greater than forecast, there are an estimated 300 million tonnes of nickel in current and future deposits accessible globally, with around another 300 million tonnes available offshore. The metal is currently mined in more than 40 countries around the world, so there is also little geopolitical risk to resources.
And it is relatively inexpensive.. Nickel is presently quoted at just twice the price of copper on the London Metal Exchange.
Why nickel is fundamental to electric vehicle batteries
While a number of different technologies are being explored for use in electric vehicle batteries, two in particular are considered the front runners, because of greater efficiency and ease of manufacturing.
Both of these are nickel-based, comprising nickel/manganese/cobalt (NMC) or nickel/cobalt/aluminium (NCA). “The cathode in the NMC-type battery is comprised of about 30 per cent nickel, that in the NCA battery is about 80 per cent nickel. In fact, while the two battery technologies are both called lithium-ion, nickel is by far the largest element in each of them,” Mistry said.
Nickel is fundamental to the development of the electric vehicle market because it is the most important element in increasing a battery’s energy density, which determines battery power and endurance.
“The more nickel we can incorporate into a battery, subject to design and manufacturing constraints of course, then the higher the energy density. For an electric vehicle, this determines the all-important issue of range,” said Mistry.
How nickel can promote recycling and the circular economy
“If we plan for production of 500,000 tonnes of nickel per annum by 2030, it is clear that the metal content is highly recyclable,” Mistry said. When a battery contains 25 to 30 kilogrammes of nickel, the metal proportion has a significant economic value at the end of its useful life, at today’s values.”
In the EU, car manufacturers presently try to store 50 to 60 kilowatt hours in an electric vehicle battery, giving a range of 120 kilometres-plus. “Since each kilowatt hour requires roughly half a kilo of nickel, then such a battery needs around 25-30 kilos of nickel. Some manufacturers are already fitting their vehicles with even stronger batteries,” Mistry said.
Nickel industry support for electric mobility in Europe
The Nickel Institute is following closely the discussions in the EU’s Battery Alliance, which is at the core of the European Commission plans to strengthen Europe’s battery industry.
“Our objective is to ensure the nickel industry has the resources to play its part in enabling and supporting the EU’s electric mobility agenda,” said Mistry. “We know that the auto industry’s ultimate target is to have an electric vehicle battery capable of supplying the same range as a tank of fuel, because that is what consumers expect.”
While new technologies are in development, at present only nickel-based batteries can supply the combination of energy density and ease of manufacturing that mass production requires, Mistry noted. Nickel really is essential to the EU’s plans for electrifying transport, he said.