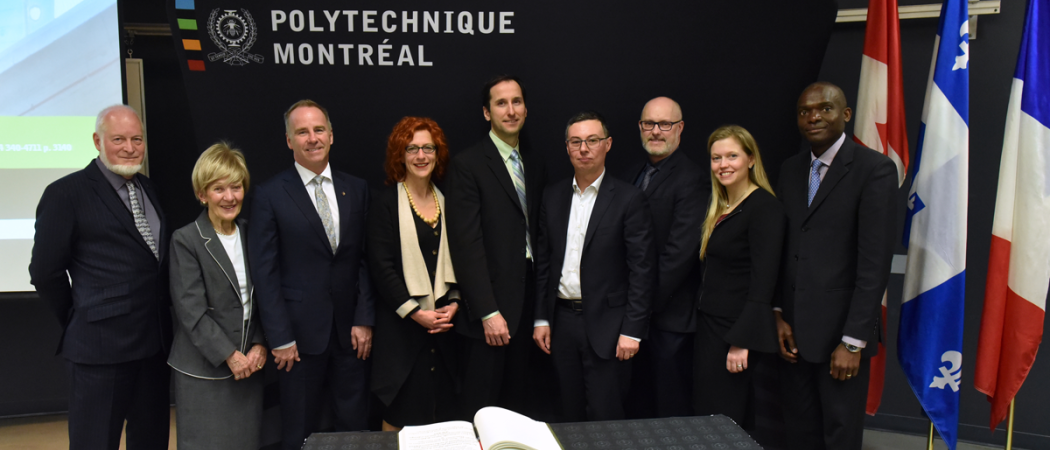
Left to right: Augustin Brais, Director of the Office of Research Partnerships and Infrastructure at Polytechnique Montréal; Michèle Thibodeau-DeGuire, Principal and Chair of the Board of Directors of Polytechnique Montréal; François Bertrand, Senior Vice-President and Vice-President of Academics and Research at Polytechnique Montréal; Annie Ross, Full Professor in the Department of Mechanical Engineering and holder of the Safran Industrial Chair on Multifunctional Passive Acoustic Treatments for Turbofan Composite Structures (TAPPIS) at Polytechnique Montréal; Daniel Therriault, Full Professor in the Department of Mechanical Engineering and holder of the Safran Industrial Research Chair on Additive Manufacturing of Organic Matrix Composites (AMOMC) at Polytechnique Montréal; Stéphane Cueille, Executive Vice-President & Chief Technology Officer, Safran; Marco Blouin, Director Science and Innovation at Ministère de l’Économie et de l’Innovation; Heidi Bandulet, Senior Programs Officer at Canada Foundation for Innovation.; Roland Fotsing, Research Associate in the Department of Mechanical Engineering at Polytechnique Montréal. (Photo: Denis Bernier)
On the strength of a decade of successful collaboration, Polytechnique Montréal and Safran, one of the largest aerospace equipment manufacturers, are announcing the creation of two new research partnerships to design a new generation of lighter, more efficient and quieter aircraft.
These projects, benefiting from multiple investments totalling $15.2 million, will involve several Montréal experts and some 80 students. After 10 years of collaboration, Polytechnique Montréal has become a strategic academic partner of Safran Group.
An international high-tech group, Safran is a leading aerospace, space and defense equipment supplier with operations in all continents and more than 92,000 employees, for sales of €21 billion (31.6 billion dollars) in 2018. Established in Canada for over 70 years, Safran is today a major player with more than 2,000 employees in five production plants and one design office.
Making lighter aircraft structures
The need for even lighter, more reliable and more corrosion-resistant aircraft is driving the aerospace industry to look at the use of new composite materials for aircraft structure, fuselage, wings and even engines.
Led by Professor Daniel Therriault of the Department of Mechanical Engineering at Polytechnique Montréal, the Safran Industrial Research Chair on Additive Manufacturing of Organic Matrix Composites (AMOMC) aims to develop the next generation of advanced manufacturing approaches and mathematical models for the creation of high-performance composite structures for the aerospace industry.
The use of geometrically optimized polymer composites will lead to huge weight savings in aerospace, which in turn will yield substantial economic and environmental benefits. This research will use thermoplastic composites as green materials, and the innovative AM processes that will be developed will have applications in other fields, particularly in the automotive industry and in construction.
Innovative acoustic materials
Population densification near airports and ever-increasing air traffic are leading to a significant rise in noise pollution caused by takeoffs and landings. The situation is so worrisome that governments have made it a public-health issue, toughening regulations in this area. Aircraft and engine manufacturers are therefore making significant efforts to design innovative devices to replace current acoustic treatments, whose performance has peaked.
Led by Professor Annie Ross of the Department of Mechanical Engineering at Polytechnique Montréal, the Safran Industrial Chair on Multifunctional Passive Acoustic Treatments for Turbofan Composite Structures (TAPPIS) aims to provide advanced multifunctional materials to absorb and dissipate the noise produced by aircraft engines. The knowledge and materials that will be developed will have economic benefits in the Canadian aviation industry and will also pave the way for applications in the rail transportation, civil construction and green-energy production sectors, among others.
Safran Group is currently collaborating with other Polytechnique Montréal teams in various research areas. These projects focus on the following topics: surface treatments with Professor Jolanta Ewa-Sapieha, prestressing treatments with Professor Martin Lévesque, microstructure analyses with Professor Gilles L’Espérance, innovative ceramics with Professor Sylvain Turenne, and health monitoring with Professors Yvon Savaria and Mohamad Sawan.
Safran and Polytechnique are already discussing future collaborations on emerging and innovative technologies, particularly in the areas of life-cycle analysis and environmental impact.
Safran and Polytechnique, a decade of successful collaborations
Thanks to the expertise, scientific innovations and unique technologies developed by Professors François Trochu and Edu Ruiz, Polytechnique Montréal became an internationally recognized research hub in the field of composite materials in the early 2000s.
Polyflex, a flexible-injection process patented by Polytechnique Montréal that enables high-performance composite parts to be manufactured in a reliable and automated manner, attracted Safran’s attention over a decade ago when the Group was looking to speed up its research to control the new structural-composite manufacturing processes, in particular for large parts. The fast-paced research led to promising results and enabled Safran to develop a better understanding of material behaviour. For its part, Polytechnique has found in Safran a strong and present partner to advance global scientific knowledge in key areas, train its students in practical industrial issues and lay the scientific foundation for new applications in several fields.
Over the past decade, collaborations have intensified and Polytechnique Montréal now supports Safran in an innovation process focused on the development of emerging and differentiating technologies.
Research in the field of composite materials contributed to the development of the fan blades for the LEAP engine, commissioned in 2016. The collaboration also led to the creation of a spinoff company in the Greater Montréal area (Ruiz Aerospace Manufacturing) as well as the advancement of scientific knowledge through the publication of some 70 scientific articles and many disclosures and patent applications.
“Safran has been a major player in, and privileged witness to, Polytechnique Montréal’s contribution to aeronautical engineering for a decade,” says François Bertrand, Senior Vice-President and Vice-President of Academics and Research at Polytechnique Montréal. “As a major player, the group was able to see the potential of our teaching and research resources by participating in bold projects in a spirit of innovation and collaboration. Safran has also witnessed the tangible impact of these projects on its solutions and processes, as well as on the know-how of dozens of students and interns, who are now driving forces of the growth of aeronautics. The industrial chairs we are announcing today are a perfect illustration of the relevance of combining academic research interests with those of industrial research to meet the evolving technological, environmental and societal needs of a top-tier industrial leader.”
“As part of a strong and lasting partnership, the men and women of Safran and Polytechnique are exploring innovative technological channels for tackling industry’s great environmental challenges of the future,” says Stéphane Cueille, Executive Vice-President & Chief Technology Officer at Safran. “The two chairs we are inaugurating today will support the joint research being conducted for the past 10 years, with the goal of developing disruptive technologies in the aerospace field.”
Incubator for new experts
The partnership between Safran Group and Polytechnique Montréal is a unique training environment. According to Joffrey Renaud, who participated in research between 2012 and 2016 while completing a master’s and PhD in the field of composite materials at Polytechnique Montréal, students benefit from this collaboration of exceptional research means, in addition to having special access to Safran’s data and specialists. This knowledge of the industrial world is now very useful to Mr. Renaud, who directs the research activities of Argon 18, a manufacturer of high-performance bikes located in Montréal.
Over the past 10 years, upwards of 150 students have, like Mr. Renaud, benefited from the close collaborations between Safran and Polytechnique Montréal. The two research chairs announced today will in turn train 80 students from all university levels in highly sought-after areas relevant to the needs of Canadian industry, primarily in transportation and aerospace.
Concerted support for research activities
The TAPPIS Chair is supported both in funding and resources by Safran Group in the amount of $1.2 million, and by NSERC, which is granting $1.1 million under the CRD grants program. Montréal-based company MËKANIC and the Centre de développement des composites du Québec (Québec composites development centre — CDCQ) are also collaborating on the equipment design and testing.
Safran Group is supporting the research activities of the AMOMC Chair by investing $2.5 million in funding and resources over five years. The Natural Sciences and Engineering Research Council of Canada (NSERC) Collaborative Research and Development (CRD) grants program is also providing $2.4 million in funding. A joint grant from the Canada Foundation for Innovation (CFI) and the Québec Government (~$8 million) has enabled the purchase of major equipment that will be used to advance the research of Daniel Therriault and other professors. It should be noted that local SMEs, including MËKANIC, will also be contributing to the chair’s activities.
“NSERC’s research partnerships support collaborations that create new scientific evidence benefiting Canada and Canadians on the economic, social and environmental levels,” says Marc Fortin, Vice-President of Research Partnerships at the Natural Sciences and Engineering Research Council of Canada. “By developing new composite materials and advanced deposition processes, this project will help further reduce the weight of airplanes, resulting in safer mass transit and greener aircraft.”
“Building lighter, more environmentally friendly planes will be groundbreaking for the aerospace industry, and for the health of our planet,” underlines Roseann O’Reilly Runte, President and CEO of the Canada Foundation for Innovation. “These types of collaborations between industry, colleges and universities push the limits of our understanding and lead to a better future for everyone.”
“The Government of Québec is proud to support the development of the aerospace industry, which is so important for the diversity of our economy, by investing in research and training,” declares Jean-François Roberge, Québec's Minister of Education and Higher Education. “Hundreds of students who are now engineers or researchers have benefited from the partnership between Polytechnique Montréal and Safran to become key players in this cutting-edge sector. Their knowledge and know-how are resonating around the entire planet. May this collaboration continue for a long time to come!”