Recycling could help with one of Europe’s toughest strategic raw material challenges, but multiple issues must be solved if the ecosystem is to thrive
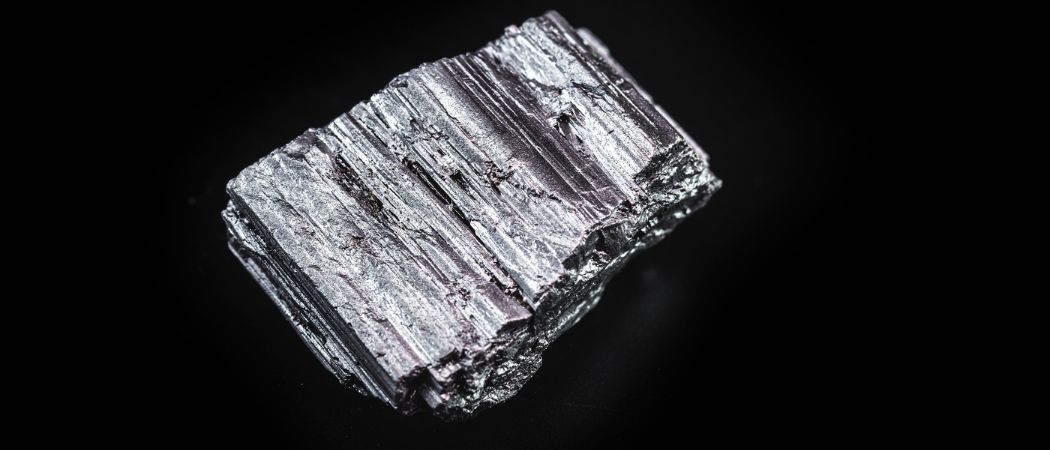
Neodymium, a magnetic chemical element considered a rare earth metal. Photo: BigStock
Recovering critical raw materials from rare earth magnets is relatively straightforward, but a number of other issues need to be resolved before a useful recycling system can emerge in Europe.
The Critical Raw Materials Act, currently making its way through the EU legislative process, addresses some of the barriers, but others need to be tackled before all the pieces fall into place.
Most permanent magnets, especially those with the highest performance, contain raw materials that are scarce in Europe. With the use of these magnets on the rise, particularly in green technologies such as wind turbines and electric vehicles, Europe is keen to break its dependence on imports, the bulk of which come from China.
For recycling to make an impact, it’s not just the recycling technology that requires attention, but the whole value chain for rare earth magnets. That stretches from processing the recycled material through to magnet fabrication. Then there have to be end users who are willing to buy magnets from a European producer rather than from China.
“There are already a lot of magnets in Europe that are collected by scrap dealers and sent back to China for recycling,” said Ana Maria Martinez, a senior research scientist at the independent research organisation SINTEF in Norway. “If we want to keep that material in Europe, the whole value chain has to talk together.”
Martinez was the project manager for REE4EU, a Horizon 2020 project that set out to demonstrate a closed-loop permanent magnet recycling process for the first time in Europe. Concluding in 2019, the project successfully treated several tonnes of process wastes and end-of-life products containing rare earth elements, resulting in the recovery of almost 100 kilograms of rare earth alloys. This alloy was then used to make new permanent magnets to be used in products.
While the recycling technology worked, taking it to the market presented further challenges. “The recyclers that we approached with our business case wanted to know: can I get 1,000 tonnes of spent magnets coming to my plant every year? And we didn’t know the answer to that,” Martinez said.
Rare earth magnets can be found in a wide range of products, from medical imaging devices and industrial robots, to consumer products such as dishwashers and microwaves. The first problem is knowing which of them contain rare earth magnets. “In most cases, until you open up the product, you don’t have a clue,” said Martinez.
The next problem is getting the magnets out of end-of-life products, most of which have not been designed to be taken apart. Doing this economically, and with due respect for the environment and worker safety, will require automation. “We cannot, in Europe, extract the magnets by hand from the different end-of-life products,” said Martinez.
Extracting magnets
These issues are being addressed in a follow-up project called REEPRODUCE, which began in May 2022 with funding from Horizon Europe. “Now we want to show that we can extract those magnets from end-of-life products in an automatised way, and that the chemical process developed in REE4EU can accommodate different magnet chemistries, from different sources,” Martinez said.
The first pilot has started, testing a sorting technology that uses computer vision and artificial intelligence to identify and pick out products likely to contain rare earth magnets from mixed electrical and electronic equipment waste.
The next stages will involve building robots that can extract the component containing the magnet from each item, and then extract the magnet itself from the component. “Then all of these magnets will go to a recycling plant, which will be robust enough to accommodate different magnet chemistries and coatings,” said Martinez.
The REEPRODUCE consortium includes 15 partners, mainly from industry, representing the whole value chain, and it will be up to them how the results are commercialised. “At the end, we’ll present some business cases for external stakeholders, but it is up to the technology owners to decide how to go further,” said Martinez.
Recycling start-ups
One of the few European start-ups in the rare earth magnet recycling is HyProMag, founded in 2018 to commercialise a hydrogen-based processing method for magnetic scrap, developed by at Birmingham University’s School of Metallurgy and Materials.
The process converts neodymium-iron-boron (Nd-Fe-B) magnets into a loose, demagnetised, hydrogenated powder. Coatings, adhesives, screws and other residues can be mechanically separated from the powder, making it suitable for immediate use in magnet fabrication.
After running a pilot plantat the university, HyProMag is setting up its first full-scale facility for remanufacturing rare earth magnets, with production due to start by the end of this year. A second facility being set up at Pforzheim near Stuttgart, by a German sister company, is expected to begin production at the end of 2024.
The production capacity of these plants is expected to be 100 tonnes of recycled NdFeB powders, alloys and magnets per year. “That’s tiny compared to the 230,000 tonnes produced last year in China, but it’s a start, and all of our technology is fully scalable,” said Carlo Burkhardt, co-founder HyProMag in Germany and scientific director of the Institute for Precious Metals and Technology at Pforzheim University. The company intends both to market the powder and alloys, and make magnets itself.
As well as the magnet recycling process, HyProMag has invested a lot of effort in developing systems to analyse and sort waste streams, and to automatically dismantle end-of-life electronic equipment.
“We’ve found some quite clever ideas for sorting ferrite magnets from Nd-Fe-B magnets, for getting magnets out of hard disk drives, and disassembling traction motors to the point where the material is suitable for hydrogen processing,” said Burkhardt
Currently part of HyProMag’s facilities, these sorting and dismantling systems could be located further up the waste stream, for example at recycling sites or with manufacturers operating buy-back schemes.
Burkhardt has seen growing interest in magnets from the recycling sector. “A couple of years ago, magnets were just a nuisance. They cause problems in shredding, they agglomerate, and they contaminate other material streams,” he said. “So, the separation is not only about recovering the magnets, but it can increase the value of the other recycled materials.”
Other barriers to the development of the sector in Europe include bureaucracy and permitting, some of which should be addressed by the Critical Raw Materials Act. But subsidies are a major headache, with companies in China and the US receiving substantial government support. “We need to have the same conditions in Europe as our competitors, given the strategic importance for European growth and for the green transition,” said Burkhardt.
The image of recycled rare earth magnets also needs to improve, although there is some movement on this front. “End users now realise that we can recycle and produce magnets that are the same as before, or perhaps even better,” Burkhardt said.
One of the biggest barriers in Europe is the lack of a skilled workforce, with only limited coverage of magnets in higher education. “No one has Nd-Fe-B as a study subject, for example, nor how they are made, nor their applications, while in China 2,500 engineers [specialising in magnets] graduate every year. In order to develop this market, we need to develop these experts.”
This is something that Burkhardt is working on as coordinator of REEsilience, a Horizon Europe project that aims to build a more resilient and sustainable supply chain for rare earth magnetic materials and products in Europe. “One of our tasks is to develop a syllabus for magnet experts, not only looking at production aspects, but also the wider framework of magnet use and recycling,” he said.
Dedicated assessment
As it stands, these methods face an economic challenge if they are to compete with the rare earth magnets produced cheaply in China. This is where the Critical Raw Materials Act will have decisive effect. The Commission proposed that at least 15% of the EU's annual consumption of all strategic raw materials should come from recycling, a level increased to 20% by the Council of Ministers. A minimum recycled content for rare earth magnets will also be set, after a dedicated assessment of the appropriate level and likely impacts.
The Act will also introduce detailed product labelling requirements, including information on the amount, type and chemical composition of magnets installed, their location and the coating, glues and additives used and how to remove them from the product.
“If we really want to have a rare earth value chain in Europe, from secondary resources, the regulatory framework has to be in place to facilitate that,” said Martinez. “Maybe it will be more expensive to recycle than to buy a magnet from China, but if it is required by law, then we are all on a level playing field and we can do it.”
Even so, Burkhardt thinks the entry costs are too high for many more rare earth magnet recycling start-ups to emerge in Europe. “About $100 million in funding was needed to develop the HyProMag technology to the level where it is industrially feasible,” he said. “That’s not like a software start-up, where you just need a couple of computers and a good idea.”
But opportunities may develop in future, as the market matures. “Currently the market is not developed, so companies need to be integrated, but in the years to come there may be much more specialisation, with companies carrying out magnet extraction, powder processing, or magnet production.”
Meanwhile established industrial companies such as Solvay and Suez are taking an interest, as are rare earth mining companies. HyProMag itself is being acquired by Maginito, a recycling technology company owned by Canadian rare earth mining concern Mkango, which was a partner since the start-up’s formation.
Elsewhere in the Ecosystem…
- Kerecis, an Icelandic scale-up using fish skin to make wound care products, is to be acquired by Danish medical device manufacturer Coloplast in a deal worth up to $1.3 billion. This valuation makes Kerecis, which was founded in 2007, Iceland’s first unicorn company. Following the expected acquisition, which is subject to regulatory approval, Kerecis will operate as a stand-alone business under its own identity and brand.
- Nine of the UK’s largest pension funds have agreed to allocate 5% of assets in their default funds to unlisted equities by 2030, a move expected to benefit start-up and scale-up companies. The government, which announced the deal on Monday, wants all defined contribution pension schemes in the UK to follow suit. This could unlock up to £50 billion of investment in high growth companies, it says.
- Irish start-up Lios has won the SME prize in the 2023 European Inventor Awards, run by the European Patent Office. Founded in 2009, the company has developed a thin, lightweight composite material for use in noise reduction applications. Arenewable diesel fuel developed by Finnish company Neste picked up the industry award, while a hydrogen storage method developed at CNRS, and later licensed to industry, won the research award.